Discover how plastic extrusion boosts production efficiency
A Comprehensive Guide to the Refine and Benefits of Plastic Extrusion
In the vast realm of manufacturing, plastic extrusion becomes a necessary and extremely efficient procedure. Transmuting raw plastic into constant accounts, it satisfies a variety of industries with its amazing convenience. This overview aims to elucidate the detailed actions entailed in this approach, the kinds of plastic proper for extrusion, and the game-changing benefits it brings to the industry. The ensuing conversation guarantees to unfold the real-world influences of this transformative procedure.
Understanding the Fundamentals of Plastic Extrusion
While it might appear facility in the beginning glance, the process of plastic extrusion is basically straightforward - plastic extrusion. It is a high-volume production strategy in which raw plastic is melted and formed right into a continual account. The procedure begins with the feeding of plastic material, in the type of pellets, granules, or powders, right into a warmed barrel. The plastic is after that melted using a mix of warm and shear, applied by a turning screw. When the molten plastic gets to completion of the barrel, it is forced via a small opening understood as a die, forming it into a preferred type. The designed plastic is after that cooled down, solidified, and reduced right into desired lengths, completing the process.
The Technical Process of Plastic Extrusion Explained
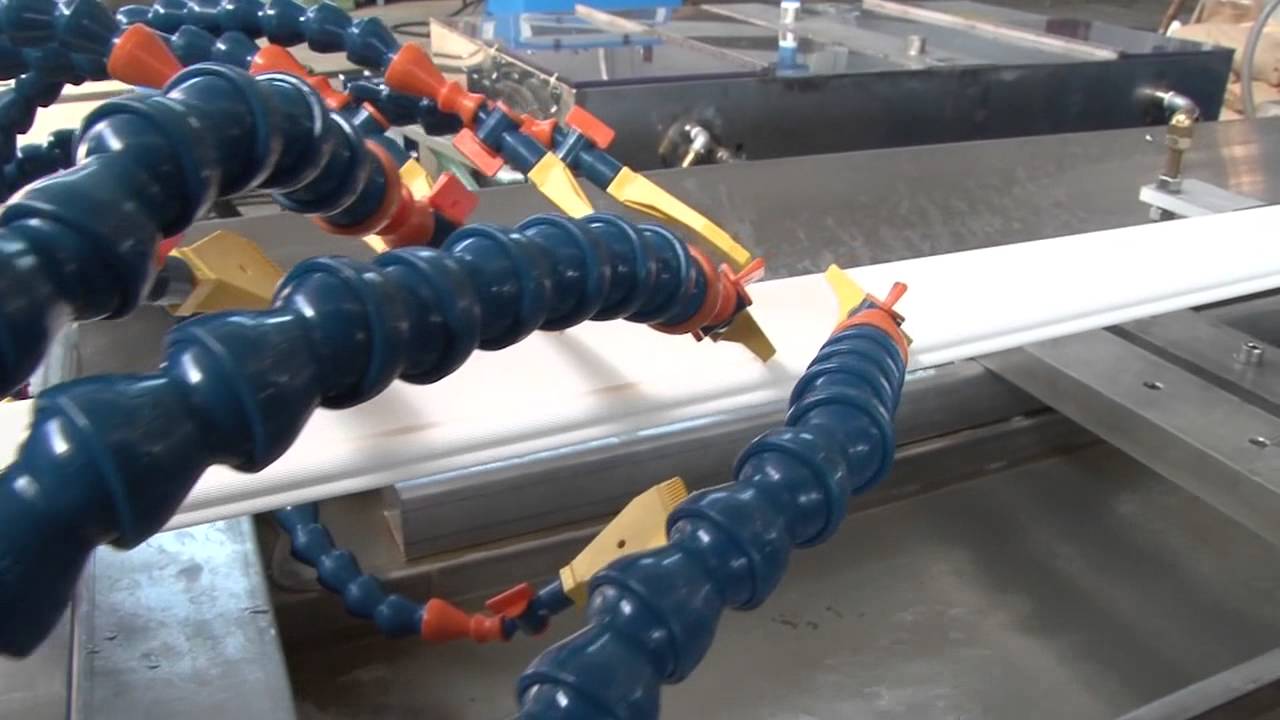
Kinds Of Plastic Suitable for Extrusion
The choice of the ideal type of plastic is a crucial element of the extrusion procedure. Different plastics offer unique residential properties, making them much more fit to particular applications. Polyethylene, for example, is typically made use of because of its low cost and easy formability. It offers outstanding resistance to chemicals and moisture, making it optimal for items like tubes and containers. In a similar way, polypropylene is another popular choice because of its high melting point and resistance to tiredness. For more robust applications, polystyrene and PVC (polyvinyl chloride) are commonly chosen for their toughness and toughness. Although these are common alternatives, the selection ultimately depends on the particular demands of the item being created. So, comprehending these plastic kinds can dramatically enhance the extrusion process.
Contrasting Plastic Extrusion to Various Other Plastic Forming Methods
Comprehending the types of plastic appropriate for extrusion leads the way for a broader discussion on how plastic extrusion piles up against various other plastic forming methods. These consist of shot molding, blow molding, and thermoforming. Each technique has its one-of-a-kind uses and benefits. Injection molding, as an example, is exceptional for producing elaborate parts, while blow molding is ideal for hollow things like containers. Thermoforming excels at developing huge or shallow parts. Nonetheless, plastic extrusion is unequaled when it involves developing continual profiles, i was reading this such as gaskets, pipes, and seals. It also enables a constant cross-section along the length of the item. Hence, the choice of technique mostly relies on the end-product needs and specifications.
Trick Advantages of Plastic Extrusion in Manufacturing
In the world of production, plastic extrusion provides lots of significant advantages. One notable benefit is the cost-effectiveness of the procedure, that makes it a financially attractive manufacturing approach. Additionally, this technique offers exceptional product adaptability and enhanced manufacturing rate, consequently raising total production performance.
Cost-Effective Production Approach
Plastic extrusion leaps to the leading edge as an affordable manufacturing method in manufacturing. This procedure sticks out for its capability to generate high volumes of product rapidly and effectively, giving suppliers with significant financial savings. The primary expense advantage is the capacity to utilize much less expensive basic materials. Extrusion makes use of thermoplastic products, which are much less pricey compared to metals or ceramics. Additionally, the extrusion procedure itself is relatively easy, decreasing labor prices. Furthermore, plastic extrusion calls for much less power than standard production techniques, adding to reduced functional costs. The process also decreases waste, as any kind of excess or faulty materials can be recycled and reused, giving an additional layer of cost-effectiveness. Overall, the economic benefits make plastic extrusion a highly eye-catching alternative in the production sector.
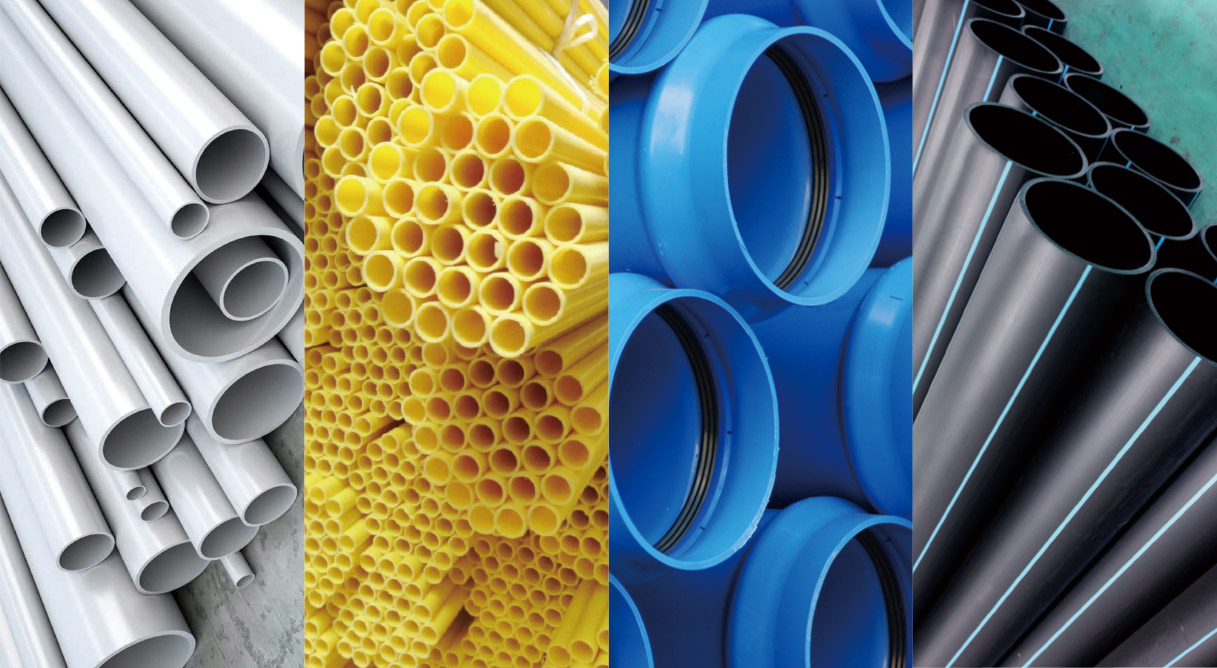
Superior Product Versatility
Beyond the cost-effectiveness of plastic extrusion, another substantial benefit in manufacturing depend on its premium item adaptability. This process permits the development of a broad range of products with differing layouts, sizes, and forms, from simple plastic sheets to complex profiles. The versatility is credited to the extrusion die, which can be tailored to generate the desired item design. This makes plastic extrusion a perfect option for industries that require customized plastic components, such as automotive, construction, and product packaging. The capability to generate varied items is not only beneficial in conference details market demands yet additionally in making it possible for suppliers to explore brand-new line of product with marginal funding financial investment. Basically, plastic extrusion's item flexibility fosters development while improving operational performance.
Boosted Production Rate
A considerable advantage of plastic extrusion exists in its boosted manufacturing speed. Couple of various other manufacturing procedures can match the rate of plastic extrusion. Furthermore, best site the capability to preserve consistent high-speed production without compromising item quality sets plastic extrusion apart from other why not try this out techniques.
Real-world Applications and Effects of Plastic Extrusion
In the realm of manufacturing, the method of plastic extrusion holds profound value. This process is widely used in the production of a range of items, such as plastic tubing, window frames, and weather condition removing. As a result, it greatly affects fields like building, product packaging, and vehicle markets. In addition, its influence includes daily things, from plastic bags to toothbrushes and non reusable cutlery. The economic advantage of plastic extrusion, primarily its high-volume and cost-effective outcome, has revolutionized production. The environmental impact of plastic waste continues to be a problem. The industry is persistently striving for technologies in biodegradable and recyclable materials, showing a future where the advantages of plastic extrusion can be maintained without endangering environmental sustainability.
Conclusion
Finally, plastic extrusion is a effective and extremely reliable method of changing resources right into varied items. It offers countless advantages over various other plastic developing methods, consisting of cost-effectiveness, high result, minimal waste, and design flexibility. Its impact is profoundly felt in different markets such as building and construction, automobile, and durable goods, making it a crucial process in today's manufacturing landscape.
Delving deeper right into the technical procedure of plastic extrusion, it begins with the option of the proper plastic material. As soon as cooled, the plastic is cut into the called for sizes or injury onto reels if the product is a plastic film or sheet - plastic extrusion. Contrasting Plastic Extrusion to Other Plastic Forming Approaches
Comprehending the types of plastic appropriate for extrusion leads the method for a more comprehensive discussion on how plastic extrusion stacks up versus other plastic forming approaches. Couple of various other manufacturing procedures can match the speed of plastic extrusion.